Effect of variable chipping clearance and operational speed on the cassava chip geometry
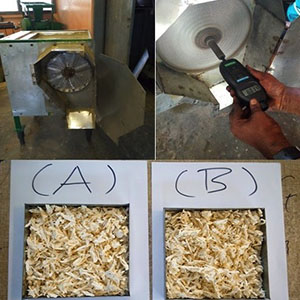
All claims expressed in this article are solely those of the authors and do not necessarily represent those of their affiliated organizations, or those of the publisher, the editors and the reviewers. Any product that may be evaluated in this article or claim that may be made by its manufacturer is not guaranteed or endorsed by the publisher.
Authors
Most cassava chipping machines adopt the fixed chipping clearance at different speeds accounting for inconsistencies in chip geometries. These irregularities influence drying time and may cause fermentation, culminating in poor quality and safety of dried chips. The need to develop a variable chipping machine capable of producing varied chip sizes for different uses necessitated this research. The main objective of this study was to develop and test the impact of a cassava chipping machine with a variable clearance and varying cutting speed on chip geometry. Drum operation speeds of 460 rpm, 730 rpm, and 800 rpm, and chipping clearances of 6 mm, 18 mm, and 28 mm were considered in this study. The study considered two twelve-month maturing varieties of cassava. These varieties were the Ampong (an improved variety) and Ankrah (a local variety). Processing time was varied between freshly harvested (FH) and 48 h after harvest (48AH). The initial moisture contents of the Ampong variety were 68.1% and 65.4% wet basis for the FH and 48AH samples, respectively. The Ankrah variety recorded 66.0% and 61.0% wet basis for FH and 48AH samples, respectively. Results from the performance evaluation test indicated that operational speed and chipping clearance had a significant effect (P<0.05) on the chips’ length, width, and thickness. Ankrah variety recorded the shortest mean chip length at 6 mm clearance and 730 rpm for the FH samples. On the other hand, Ampong samples at 730 rpm and 18 mm machine clearance recorded the shortest mean chip length for the 48AH samples.
How to Cite

This work is licensed under a Creative Commons Attribution-NonCommercial 4.0 International License.