Simulation study and field experiments on the optimal canopy shaking action for harvesting Camellia oleifera fruits
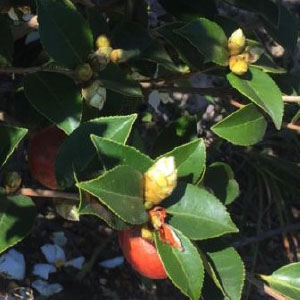
All claims expressed in this article are solely those of the authors and do not necessarily represent those of their affiliated organizations, or those of the publisher, the editors and the reviewers. Any product that may be evaluated in this article or claim that may be made by its manufacturer is not guaranteed or endorsed by the publisher.
Authors
With the increasing cultivation scale of Camellia oleifera in China, the demand for mechanical harvesting machinery is very urgent. Inefficient fruit harvesting has become a bottleneck hindering the development of the C. oleifera industry. In order to achieve high fruit harvesting percentage and low detachment percentage of the flower buds, a canopy shaking mechanism is proposed for massively harvesting C. oleifera fruits which applies the reciprocating linear motion of multiple beating-bar arrays to the tree canopy. The multiple beating-bar arrays driven by the eccentric disk can generate comb-brushing effects on the tree canopy. Three kinds of C. oleifera tree architecture were modelled, and their dynamics were simulated by finite element analysis. Their modal analysis results show that the low-order natural frequencies of the C. oleifera trees with different canopy shapes are very close. According to harmonic response analysis, the low-frequency excitation is used to harvest C. oleifera fruit. The orthogonal experiments were carried out on the canopy shaker prototype with the motor speed, reciprocating stroke, and duration of vibration as the influencing factors, and the fruit harvesting percentage and the detachment percentage of the flower buds as the evaluation indices. The results show that the same optimal parameter combination can be used for three kinds of C. oleifera tree architecture, in which the motor speed is 360 r/min, the reciprocating stroke is 80 mm, and the duration of the vibration is 8 s. The average fruit harvesting percentage is 72.3%, and the average detachment percentage of the flower buds is 13.9%.
How to Cite

This work is licensed under a Creative Commons Attribution-NonCommercial 4.0 International License.