Optimal design of transplanting mechanism with differential internal engagement non-circular gear trains
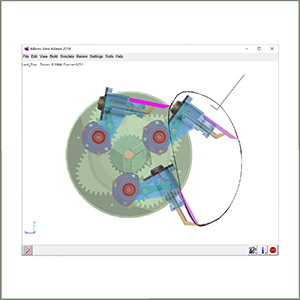
All claims expressed in this article are solely those of the authors and do not necessarily represent those of their affiliated organizations, or those of the publisher, the editors and the reviewers. Any product that may be evaluated in this article or claim that may be made by its manufacturer is not guaranteed or endorsed by the publisher.
Authors
This study aimed at the problems of unequal speed transmission ratio mutual restriction and side gap accumulation of the transplanting mechanism with single-degree-of-freedom K-H-V non-circular planetary gear train, which leads to poor trajectory and attitude, and poor precision of movement. This study has proposed a simple structure of transplanting mechanism with differential internal engagement non-circular planetary gear trains, which reconstructs the complex transplanting trajectory and attitude of the planting arm through single-stage unequal speed transmission. The working principle of the transplanting mechanism was analysed, and the kinematic theoretical model of the transplanting mechanism was established. The optimal design software for the transplanting mechanism was developed based on the visual platform. The dimensions optimisation on the transplanting mechanism was completed considering the requirements with strong coupling, and multi-objective and a set of superior mechanism parameters were obtained. The design theory and method of the internal engagement non-circular gear pair were proposed based on the generating principle. The correctness and accuracy of the trajectory and attitude of the transplanting mechanism were verified through virtual simulation experiments. The experiments show that the designed transplanting mechanism with internal engagement non-circular planetary gear trains was compact in structure, the trajectory meets the requirements of multi-objective transplanting, and the trajectory and attitude can be accurately reproduced, which provides a new feasible solution for the innovative design of the transplanting mechanism.
How to Cite

This work is licensed under a Creative Commons Attribution-NonCommercial 4.0 International License.