Design and experiment of a self-propelled two-row garlic combine harvester
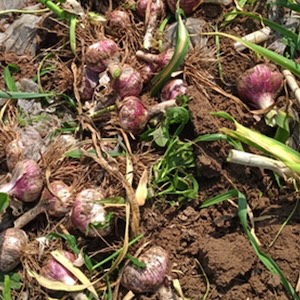
All claims expressed in this article are solely those of the authors and do not necessarily represent those of their affiliated organizations, or those of the publisher, the editors and the reviewers. Any product that may be evaluated in this article or claim that may be made by its manufacturer is not guaranteed or endorsed by the publisher.
Authors
Given the significant damage rate observed during the transportation of current garlic combine harvesters in China, this study aims to design a new garlic combine harvester capable of achieving minimal harvest losses. The designed machine can simultaneously complete operations for garlic digging, clamping transport, seedling-bulb separation, soil cleaning, and fruit collection across two rows. Through the use of theoretical analysis and calculation of garlic harvesting operations, the key parameters of soil-breaking device, clamping transport device, length-limiting cutting device, and soil cleaning conyeyor were determined. The Box-Behnken test technique was utilized within Design-Expert software, and orthogonal experiments were conducted with the unit's forward speed, digging depth, and soil-breaking angle as test factors, and the stem cutting rate and bulb damage rate as test indices. The test results showed that when the unit's forward speed, digging depth, and soil-breaking angle were 0.49 m/s, 100 mm, and 20°, respectively, the working parameter combination was the best, and the rate of stem cutting and damage were 95.71% and 3.10%, respectively. The findings from the field experiment and optimization aligned closely. This study can provide reference for the development of mechanized garlic harvesting.
How to Cite

This work is licensed under a Creative Commons Attribution-NonCommercial 4.0 International License.