Modelling, analysis, and optimisation of the rear axle of cereal combine harvester under real loads using finite elements method
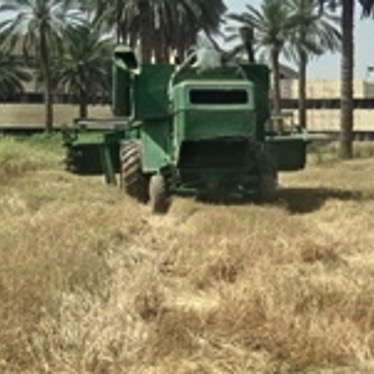
All claims expressed in this article are solely those of the authors and do not necessarily represent those of their affiliated organizations, or those of the publisher, the editors and the reviewers. Any product that may be evaluated in this article or claim that may be made by its manufacturer is not guaranteed or endorsed by the publisher.
Authors
Cereals combine harvester is one of the agricultural machines that work under challenging conditions, and different forces are applied to its parts. This study aimed to analyse static and dynamic loads on the rear axle of the JD955 combine harvester to optimise it. First, real loads on the axle were measured by a special electronic system in stationary and moving modes on roads and farms with various forward speeds. Then, a geometric model of the axle was designed in the CATIA software. Finally, the ANSYS Workbench software performed static, harmonic, transient, and dynamic analyses using the finite element method. The mean of maximum loads on the axle in stopped mode, asphalt road, dirt road, and inside the farm (while moving parallel and perpendicular to the farrows and turning in farm end) were equal to 15.067, 18.830, 49.167, 21.428, 27.07 and 27.857 KN, respectively. There was a relatively linear relationship between the axle load and deformation. At the maximum load of 49.167 KN, the maximum von Mises stresses of 1200, 85.848, 21.392, and 1.754e-14 MPa were obtained in static, transient, dynamic, and harmonic analyses, respectively. Since structural errors in the axle were numerically close to zero, the calculated stress values had good accuracy. The axle fatigue life for most loads was equal to the ideal value of 106 cycles. The least fatigue safety factor was obtained from 0.072 to 0.745 in static analysis and from 0.174 to 1.029 in linear transient analysis. According to the analysis results, it was necessary to optimise the existing axle design. So, a rectangular piece was suggested as the suitable design for the JD955 rear axle middle section.
How to Cite

This work is licensed under a Creative Commons Attribution-NonCommercial 4.0 International License.