Use of 3D scanning technique to determine tire deformation in static conditions
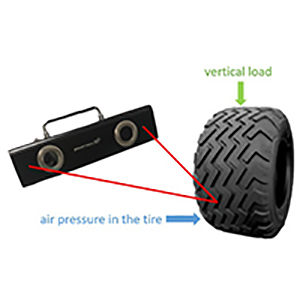
All claims expressed in this article are solely those of the authors and do not necessarily represent those of their affiliated organizations, or those of the publisher, the editors and the reviewers. Any product that may be evaluated in this article or claim that may be made by its manufacturer is not guaranteed or endorsed by the publisher.
Authors
This paper presents an innovative digital method to analyze agricultural tire profiles based on pictures. This method can conclude that vertical load and inflation pressure changes cause tire deformation. The first stage in this method is 3D scanning; the vertical cross-section is created from the obtained picture of the tested tire. From this cross-section, the deflection of the tire can be determined. Then, the horizontal cross-section is formed: this operation determines the tire’s contact area at the highest vertical deformation. Obtained results can be helpful to make the tire deformation characteristic. The contact pressure values can be determined (even through laboratory testing, without research in field conditions). The knowledge about contact pressure allows taking some actions to reduce soil compaction. In the description of the method, the radial tire was used, but the structure and equipment of the test bench allow the use of cross-ply tires with different dimensions.
How to Cite

This work is licensed under a Creative Commons Attribution-NonCommercial 4.0 International License.